Software for
Accelerating
Manufacturing
We help factories to eliminate production stops and waste, optimise factory work, save energy, transition to paperless operations, and guide through digital transformation and evolution.
Accevo SMART FACTORY
One platform. Plenty of solutions for Manufacturing Operations Management
What We Do
Accevo Systems (formerly ANT Solutions) is a one-stop provider for your manufacturing improvement needs.
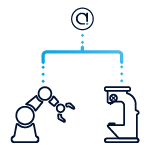
Machine
Connectivity
We collect signals from every possible machine on the market
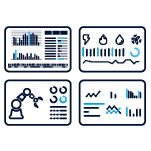
Software
Development
You get an out-of-the-box modular system ready for major customization
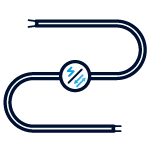
Implementation
We provide the infrastructure and do all the heavy lifting
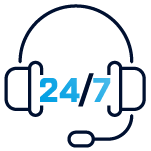
Continuous
Support
You get 24h/7 on demand support
Cloud Manufacturing
Unlock the Potential of Cloud Manufacturing: Increase Efficiency, Reduce Costs, and Enhance Product Quality. Choose between Cloud-Native and On-Premise Architecture
- Scalability
- Accessibility
- Agility and Flexibility
- Better Use of IT Resources
- Additional Cloud Services
- Improve Security
- High Availability
Continuous Improvement
Empower your solution with multiple extensions
Benefits for your production
65%
FASTER REACTION TIME
- • Real-time production data from machines
- • On-line notifications for production maintenance & quality
- • Production progress & quality online monitoring
90%
REDUCTION IN REPORTS GENERATION
- • Automatic data collection from the machines
- • Bi-directional interface with ERP
- • Digital guidance for Operators
15%
OEE INCREASE
- • Higher machines net run time
- • Microstops reduction
- • Less defects
Transform your production in 6 weeks!
We will implement the standard system in 6 weeks, thanks to out-of-the-box solution and proven implementation method
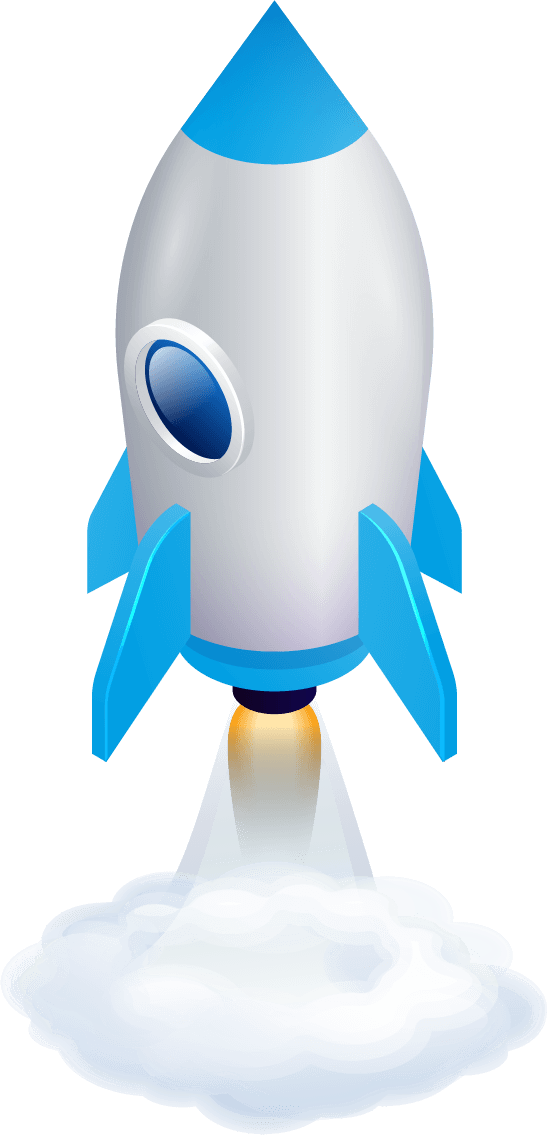
2025 Digitalisation Guide
- Learn what are the key steps to digitalise factory
- Identify key problems that occur during the production
- How software for factories fits industry 4.0 paradigms
- Why digitisation of production plants fails?
- What the MES price depends on?
- What human resources do I have to reallocate to the project?
Related articles
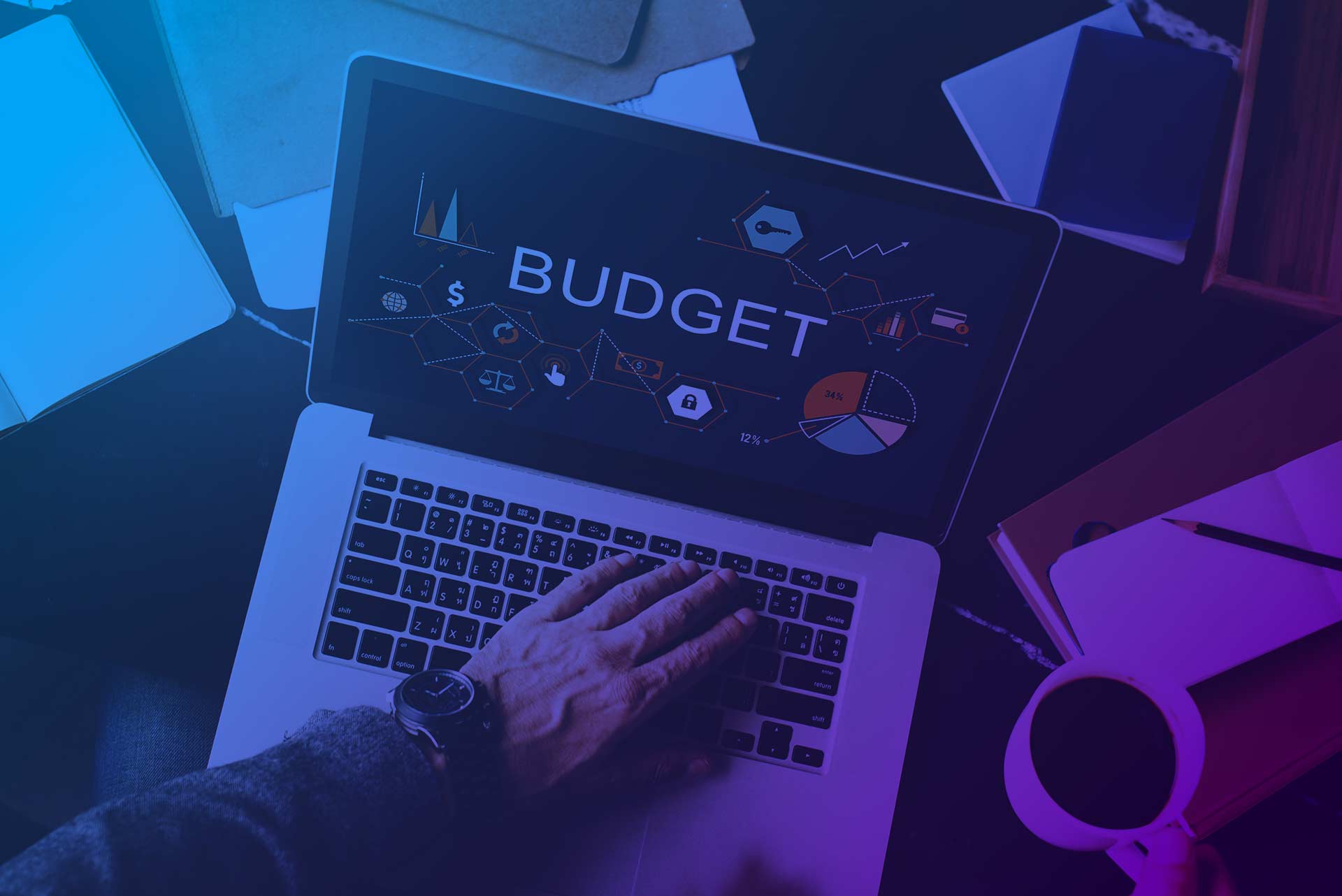
Why do MES and IT projects often go over budget?
Making the decision to implement a manufacturing execution system is just the tip of the iceberg. The next stage is to refine the details of
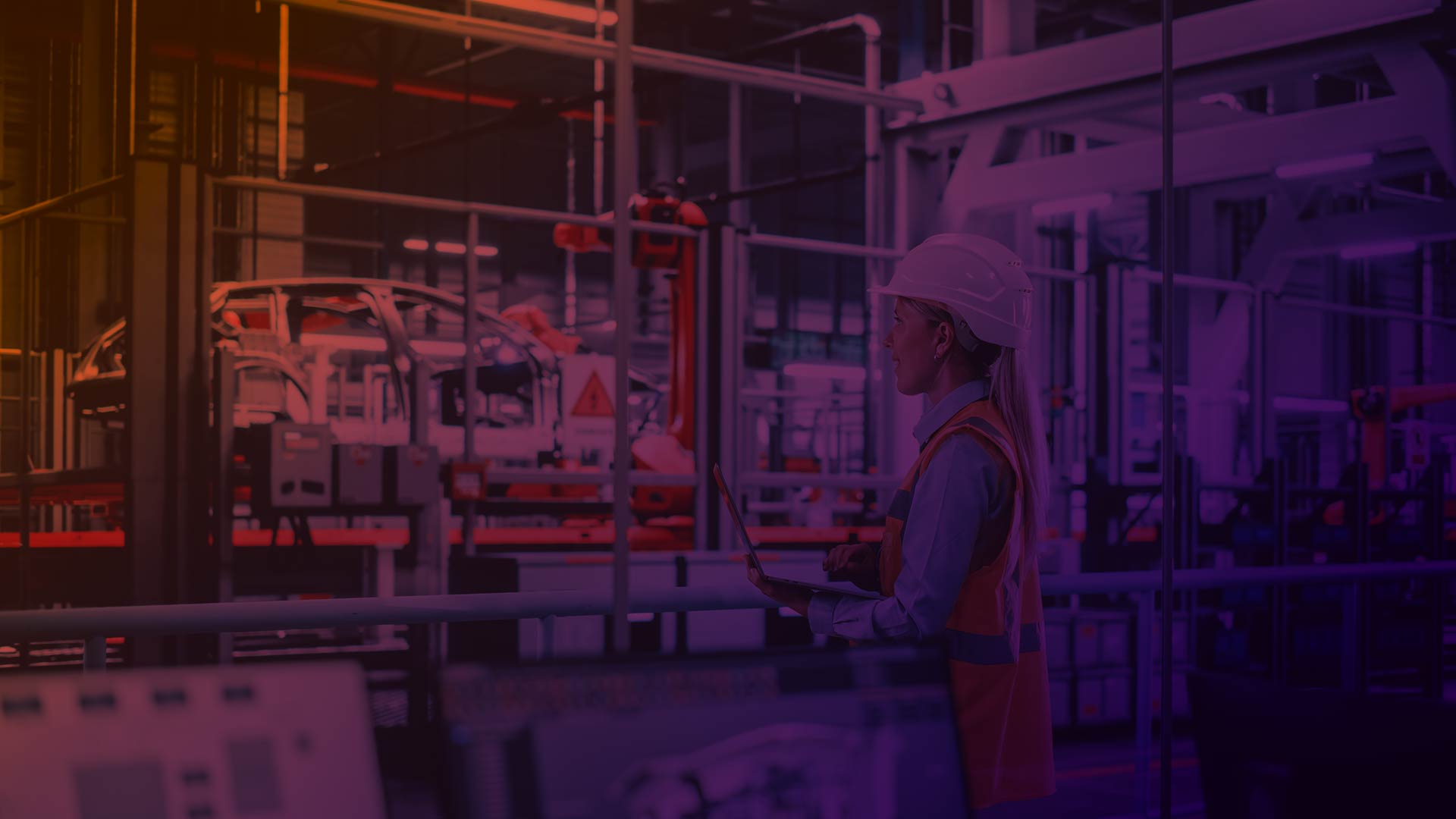
Here’s What Will Happen If You Don’t Start Monitoring Production
Neglecting production monitoring can lead to significant problems for any business. In this article, we’ll explore the consequences of not monitoring production and the benefits of implementing a monitoring system.
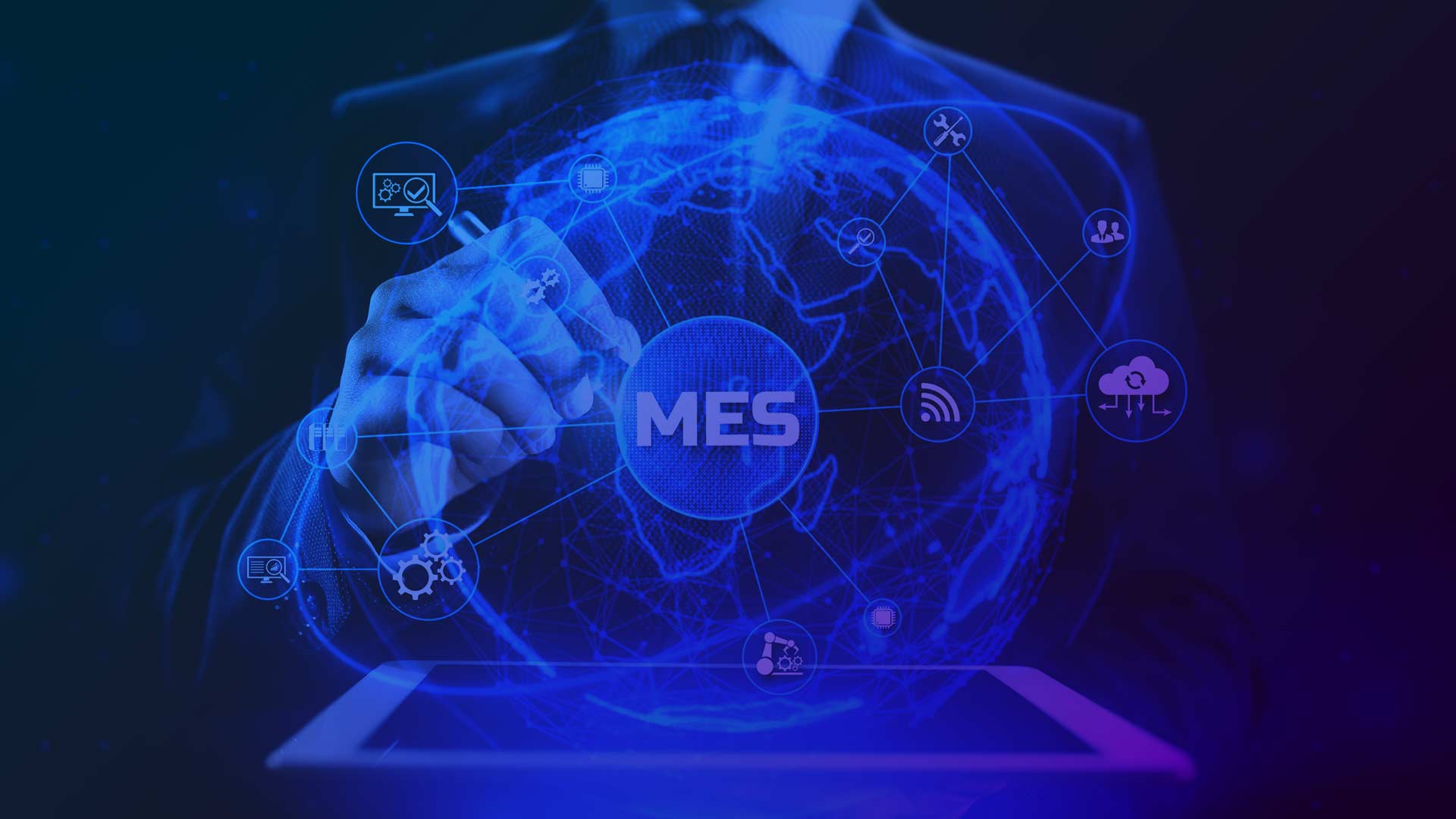
How to model production process in MES?
The successful MES implementation depends on several factors – from the correct implementation of the data being collected to the precise analysis of the information.
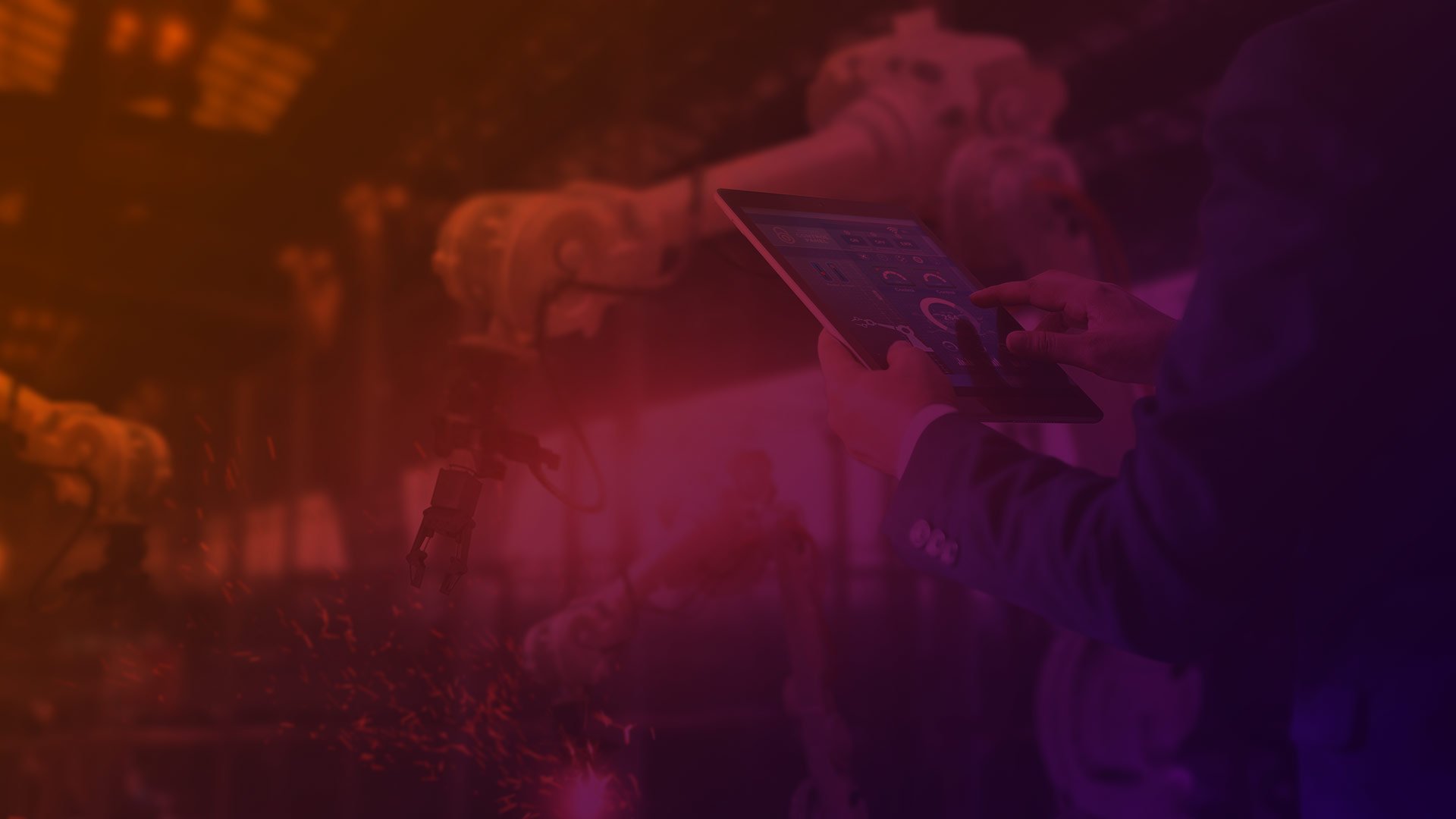
What is a Smart Factory? Simply explained
A smart factory is a manufacturing facility that uses advanced technologies to collect and analyse data, automate processes, and make decisions in real time. Smart
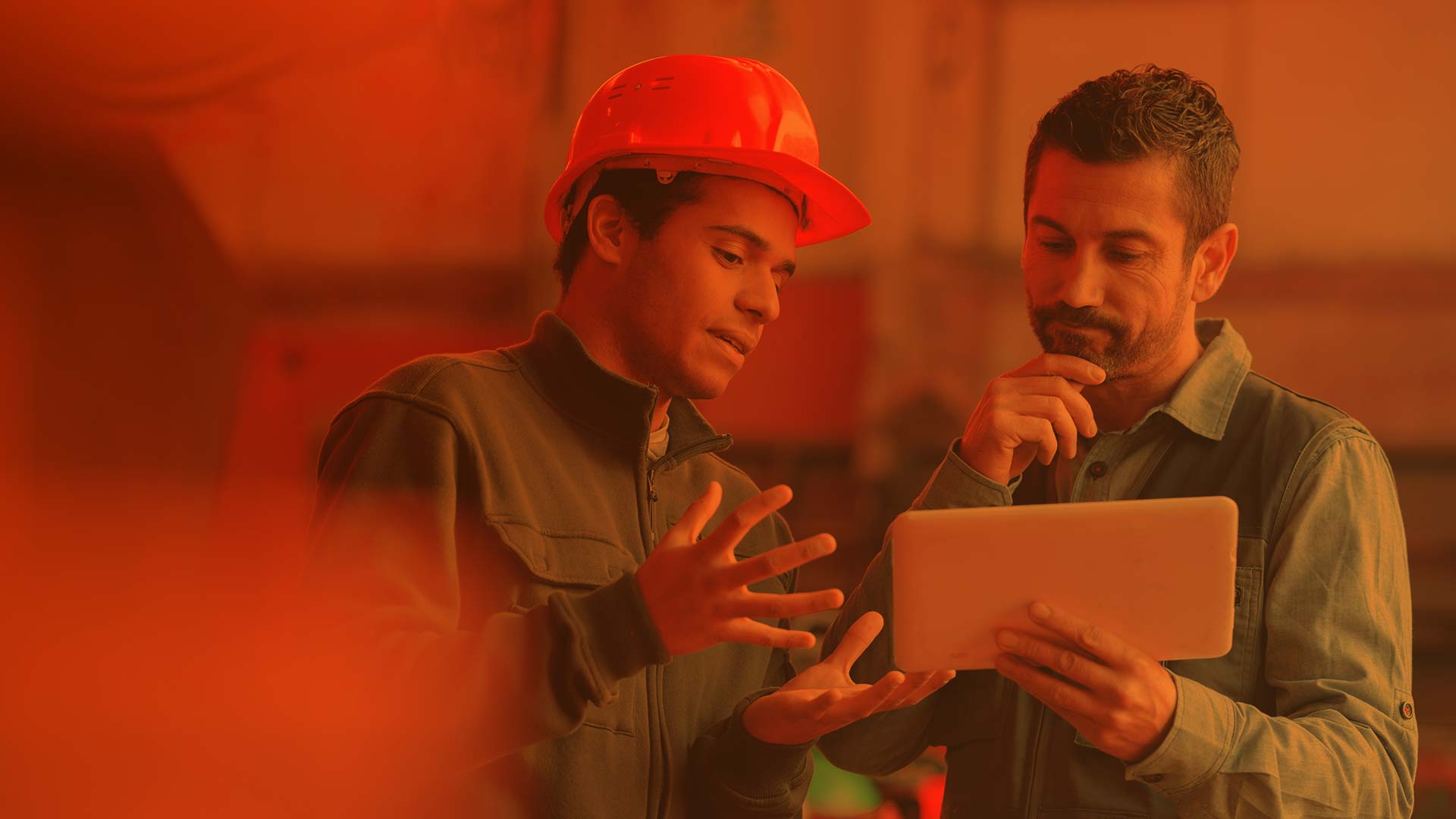
How to make your meetings on the shopfloor more efficient?
Meetings on the shopfloor are pretty much an everyday occurrence and are essential to keep things running efficiently and effectively. The type and quantity of
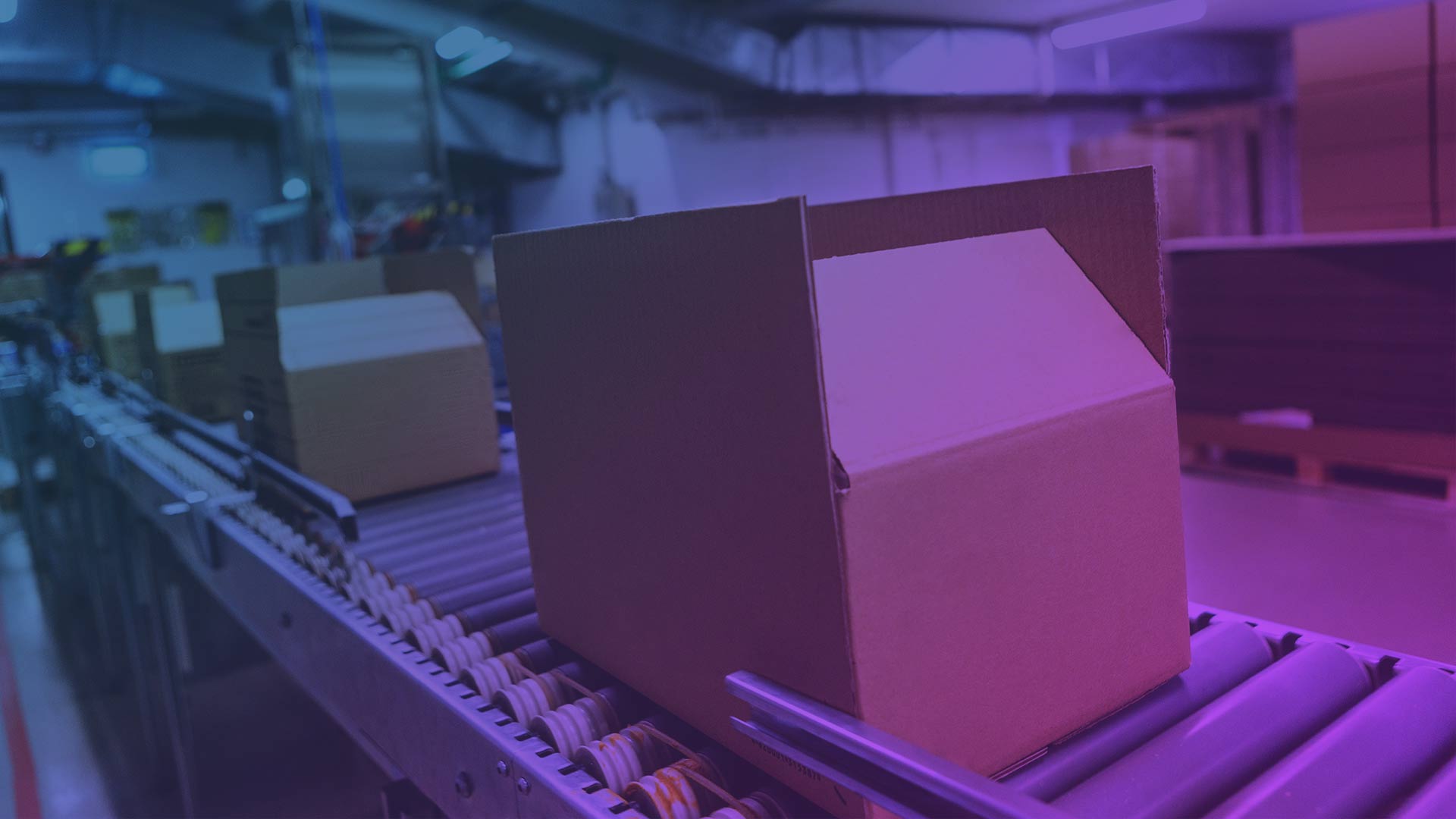
How Generic Master Batch Records (GMBRs) Can Improve Packaging Efficiency
In the pharmaceutical and manufacturing industries, Generic Master Batch Records (GMBRs) are increasingly being used to improve packaging efficiency. GMBRs are a type of master